On-Site Resource Management Using the Amage Systems Toolkit
On-Site Resource Management Using the Amage Systems Toolkit
Introduction
Resource management in the context of construction work. We describe the possibility of using the AMAGE system in the complete cycle of work execution in the context of construction work, implementation, and process monitoring.
Managing Resources on the Construction Site
There is always the pressure of time and money in construction projects. Work schedules never give the relaxation of peaceful execution of all tasks and those doing the work directly on site the comfort of the work and a sufficient margin of safety. Deadlines always chase us, and often we catch up with the progress of work, schedules, and tasks with ingenuity. We make rapid changes in the organization and work to improve communication between all participants in the process. Cost pressures are also crucial. The current trend toward giving the teams responsible for executing the work a great deal of independence in decision-making and the manner of implementation offers a potential horizon for earning more profit by completing all work efficiently and completing tasks ahead of schedule. That carries over unequivocally into a measurable financial effect for all employees.
Both time and money are simultaneously challenging, given the volatility of the construction environment and unexpected changes in the delivery process, execution, and the need for design changes. The norm is to solve thousands of problems every day, whether directly on site or in dealing with suppliers, subcontractors, and our own employees.
How Is the Construction Industry Currently Coping?
To cope with all obstacles, the site, and its environment must develop meaningful communication mechanisms, to respond to potential problems, which always occur, in the shortest possible time. The only quick and effective reaction will allow to limit losses or eliminate them. The coordinators of each area deal with such a case as best they can. Creativity is unlimited. Typically, enterprise-wide global ERP systems focus on the core financial and physical accounts. They support the procurement area, but that may be insufficient directly on the construction site. In this case, additional tools appear: task planners or ubiquitous spreadsheets to somehow control what is happening on the construction site. Everyone is interested in the progress of work and quick information about "how far we are".

Is the ERP System Sufficient for This Type of Tasks?
As previously mentioned, major/global ERP systems for construction companies are not always able to track the whole circulation, not so much financial as material on construction sites. It is common to implement the purchase and settlement area in such systems. What appears on the construction site is already included in the project's costs. In subsequent steps, the quality of information about the actual progress depends on employees' inventiveness, developed tools, and information transferred by phone/email. Given that the process involves not only our employees but subcontractors and suppliers, information can get stuck in certain places, especially when it is in the hands of those reporting. Who doesn't remember a case when a subcontractor reported positive work progress while in reality, work on the construction site did not look so rosy. A supplier reporting a planned delivery does not always meet the deadline, and the delivery differs from what we ordered.
Is the ERP System Sufficient for This Type of Tasks?
As previously mentioned, major/global ERP systems for construction companies are not always able to track the whole circulation, not so much financial as material on construction sites. It is common to implement the purchase and settlement area in such systems. What appears on the construction site is already included in the project's costs. In subsequent steps, the quality of information about the actual progress depends on employees' inventiveness, developed tools, and information transferred by phone/email. Given that the process involves not only our employees but subcontractors and suppliers, information can get stuck in certain places, especially when it is in the hands of those reporting. Who doesn't remember a case when a subcontractor reported positive work progress while in reality, work on the construction site did not look so rosy. A supplier reporting a planned delivery does not always meet the deadline, and the delivery differs from what we ordered.
Do area coordinators and site managers have any alternatives to excel sheets, e-mail exchanges, and phone calls? Is it possible to manage the process in such a way as to help provide the line workers with accurate and up-to-date information and, at the same time, the managers with the actual information from the construction site?
It seems that the answer is YES. Our solutions, developed and tested in action, allow for practical support of these processes and answer these questions in the affirmative.
Comprehensive Solution – AMAGE
The area of construction works is a broad matter. Our solutions allow for the implementation of several key processes. At the same time, they are modular enough that, depending on the organization, they can work together or be used in specific, selected areas in cooperation with existing ERP systems in order to facilitate the implementation of these works.
The easiest way to illustrate the process that AMAGE can operate is the following diagram. The presented model is comprehensive, i.e., it includes processes from the moment of the order until completion of assembly work/return of devices. At the same time, it is not 100% complete. After gathering all the information generated in these processes, we can perform maintenance work such as: verification of employee authorizations, equipment inspections, and health and safety checks. However, activities described in our maintenance solutions are more widely used and are covered in detail there. Here we will focus on the main process and its three areas: materials, internal distribution, and assembly/assembly. Each of these areas is worth discussing separately. In addition, there is a layer of data exchange, whether with ERP systems, design systems, or work support systems such as BIM.
The key in our description is the focus on the circulation of resources (assets) on the construction site. It is not just about managing tasks and their progress. In our case, the main emphasis is on the reasonable management of the assets on-site from the moment they arrive until they are built up or returned (if we are talking about rented items). Everything that arises in the meantime is vital information that we share with both the users on-site and the area coordinators/managers.
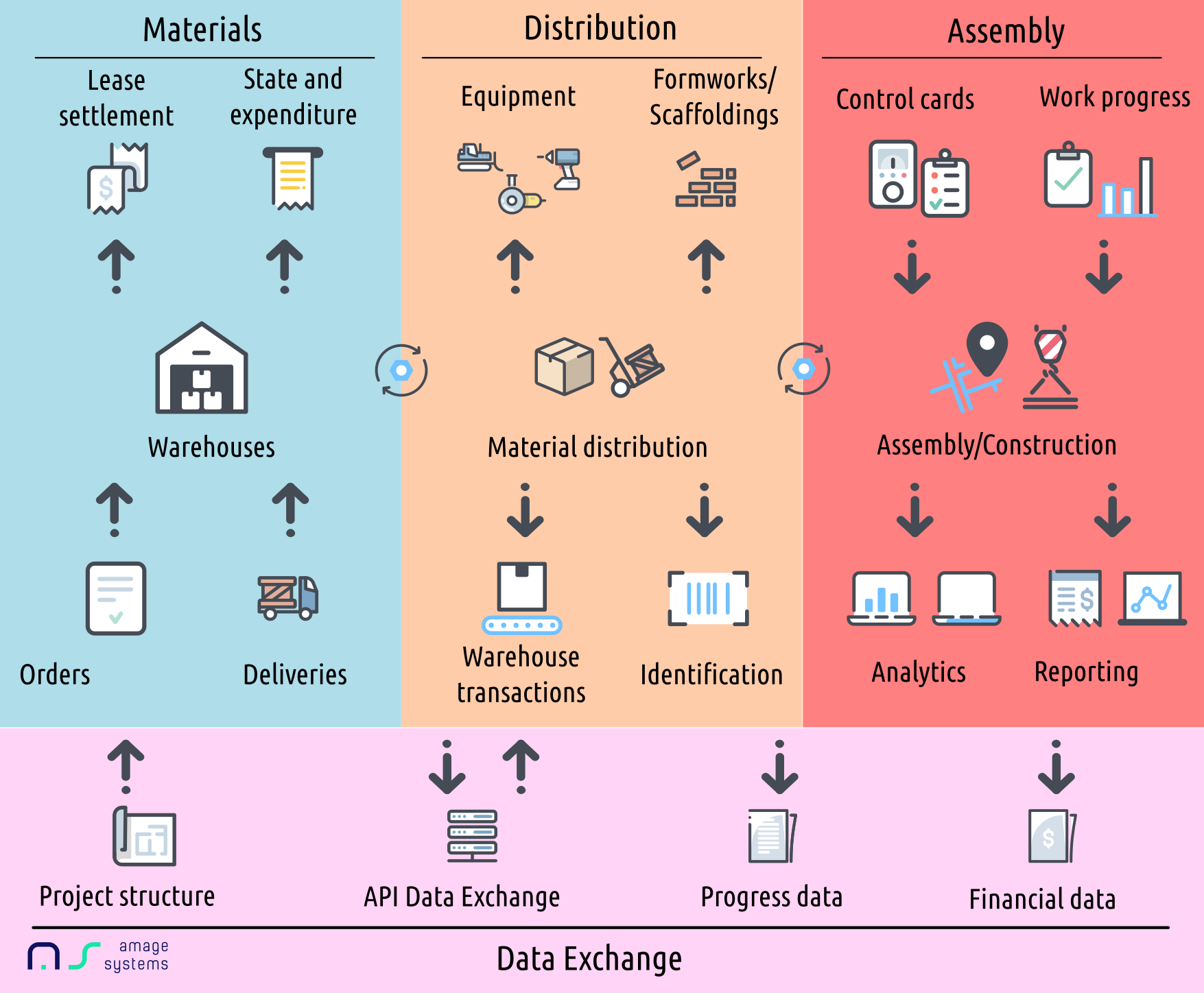
Area of Materials
This area deals with the circulation of materials from the moment of making an order, up until its transfer to internal distribution or return to the supplier (in the case of rented elements). The processes of orders, related deliveries, and returns enable the precise ordering of components. Grouping Bill of Quantity (BOQ) into contracts, objects, and construction elements facilitates the management and coordination of these activities. Deliveries/returns can be verified during delivery against the list provided by the supplier. With mobile devices, we can perform quantity and quality verification. Related claims are automatically sent to the supplier. Returns take into account the process of loading elements from different facilities/elements and then verification of transport at the supplier's warehouse. Tools supporting these processes are supplier portals, where the supplier integrates with the system by entering and verifying his own actions. Integrations via email or other integration tools allow for faster connection and transfer of information between suppliers and the construction site.
Â

All of this information provides the analytics for this step. The system generates billing information concerning elements or equipment rented from external suppliers. Specialized tools and functions for formwork/scaffolding area and rental of small equipment allow to make detailed settlements in a monthly context and to compare key stages of such processes - from the stage of the offer, through projects, to the execution of orders/returns. Settlements of stocks and history of use of elements allow for quick and precise access to the actual costs of the process. Integration with ERP systems can be implemented at any stage of this area, increasing the transparency of construction work
Area of Distribution
The distribution area covers handing the materials over in the construction area. That includes the release of construction elements from warehouses but also the distribution of equipment and machinery rented from external suppliers. The first area is supported by mobile tools and strong integration with identification mechanisms such as barcodes and proximity tags, which allow for the quick and simplified execution of these activities. The support of our offline tools makes it possible to perform these activities without access to a wireless network, which is a quite common occurrence on construction sites. Infrastructure in the area is insufficient. Often we work in conditions with shielding (concrete, steel) or in a location of warehouses (underground), which causes wireless network loss. At this stage, we can define the consumption centers, people, and activities for which materials are collected, but also we can use unique identifiers for the key elements in the context of an assembly. That allows tracking all of the processes associated with the assembly, from the collection from the warehouse to the final control works.
Rented items also find their place in this area. Linking them to subcontractors, team sections, and individual employees enables precise tracking of the rental path and tools and machines transfer between individuals with continuous tracking of cost centers. Moreover, it facilitates the process of repairs, replacements, and returns of equipment to the suppliers. Materials used in this process due to their role can be further tracked in the assembly area, which we will now discuss.
Area of the Assembly
Some areas of construction work require detailed tracking of installation activities. Usually, these are the elements of equipment of a particular building - industrial plant or other such construction. These elements require installation in compliance with the implemented design and the industry requirements (e.g., electrical work, piping work). AMAGE supports the teams in this respect by providing tools to supervise this process. From the release of the components from the warehouse, with the help of definable supervision templates, the system allows us to accurately determine the progress of the work by importing the entire project structure - broken down into areas, sections, and systems - to provide accurate information on the progress at any stage. Another advantage is the possibility of full coupling with project teams, where data import into the AMAGE system can be performed periodically with the intelligent data analysis and an indication of differences in projects and work fronts. All that facilitates billing and invoicing activities.
Assembly data is reported via mobile devices and unique elements' identifiers online and offline. With this information, area coordinators get quick information about the progress of work, plan, and actual implementation, as well as the performance of individual teams. That allows for very effective coordination of work and quick and easy settlements both at the subcontractor level and with the investor/general contractor.

The control card, analytics, and documentation modules are an addition to those works. By identifying individual resources in the system, we can provide contextual information, for instance, about a selected cable. We transform thousands of pages of documentation (e.g., terminal strip plan) into information, immediately available to all employees with basic mobile equipment. Control cards enable the implementation of the employees responsible for connecting devices/machines/pipelines into the control process. Definable templates allow us to carry out the work fully electronically, together with photographic documentation. Due to the automation of the processes, the system facilitates those activities and supervises the assembly process. All this information is available on an ongoing basis for those responsible for the implementation, enabling quick accounting and reporting.
Exchange of Data
What is important, the deployment model adopted by AMAGE Systems allows for quick and flexible implementation of particular areas on an ongoing basis during the project's execution. Data importers from spreadsheet sources allow entering historical data of already started construction projects. Integration with ERP systems facilitates further automation of work, which is especially crucial for projects where time is a key decision factor.
COVID-19 - As an Addition to DDM Procedures
In the current pandemic situation, an additional advantage of this approach in digitizing on-site processes is the increased distancing of the various teams and better coordination of the work in progress without the necessity of the constant presence of the coordinators. Digitization of those processes, intensified by COVID-19 and its consequences, is gaining new momentum. The AMAGE system is prepared for this and provides a full set of integrated tools for further support of the teams involved directly on-site.
Handling the full cycle of investment realization
Support for operational workers
Full control for area coordinators
Solution Demonstration, Implementation, and Purchase
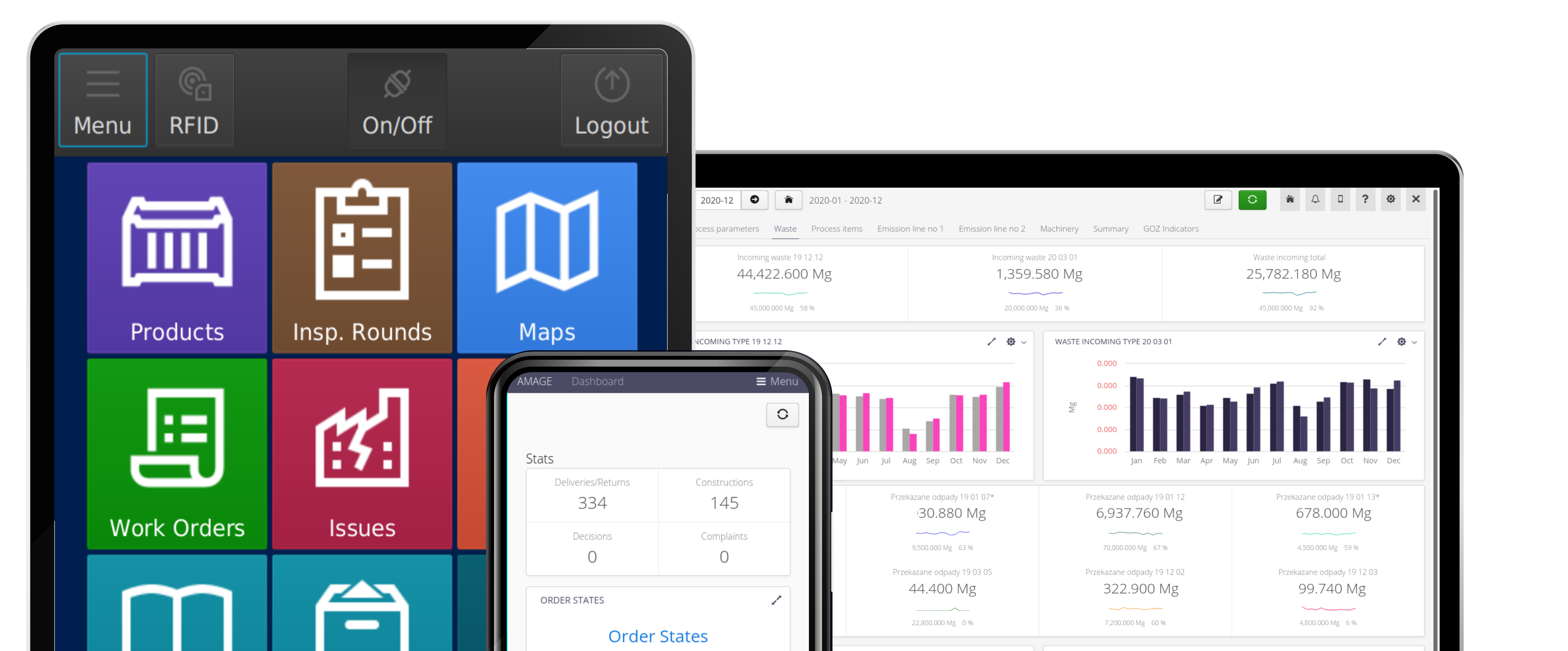