Automatization of Inspection Rounds
Automatization of Inspection Rounds as a Way of Extending Knowledge about Own Machine Park and Reducing Paper Waste
Introduction
Every production plant with its own machine park requires ensurence of continuity of appliance's work. It is especially crucial in plants with a continuous production process. We are talking about power and chemical plants, heavy industry, as well as food-processing plants. In each of them, the technological process may be continuous, meaning that disruption of the process has a negative impact. In simple terms, disruption of the process causes degradation of semi-finished products or even damage to the machines responsible for the process ( vide coke plants). Each of such disruptions equals a technological and financial risk for the enterprise.


Plants automatization is rapidly progressing. A lot of information can be received through DCS systems; however it does not apply to all data. Not all devices are equipped with sensors and data downloads automatically. Also crucial for the plant is the presence of an actual human in some areas, as they say - the master’s eye makes the horse fat. It facilitates detecting potential dangers, impossible to identify by computer systems. Due to that, almost every plant defines paths of inspection rounds. During which registered are technological information, data from specific measurement points, and observations such as visual inspection (e.g. condenser's operation). Each inspection round is marked on a timeline with a defined duration.
Maintenance department employees have to know how to cope with such tasks. Without proper tools, the employee fills in a paper report with the necessary information, then submits it to the coordinators. In case of any inconsistency/potential issue, it is reported in person or by phone and eventually ends up in archives. A couple of days after corrective action the report is forgotten, and information has historical value. Looking through and analyzing such data is difficult, as well as putting it into a spreadsheet, so almost no one undertakes this job because of the necessary effort. Handling requests are also at risk of being forgotten, or  not being appropriately done.

Other Ways
There is, however, a different approach to this issue. The work of such a system can look as follows. System coordinators define inspection rounds' paths in the application. Assign devices, checkpoints, measurements, and observation points to a checklist. Mark if certain actions require measurements (temperature measurement un point X) with instructions on necessary actions, responses to questions (lack of noise - piston pipe), and a particular task (take a picture of a device, scan RFID card in a control point). Create a schedule for each control round (every day, every 6 hours), and allow implementation with a margin of +/- 1h since employees also have other tasks. The report and technical information are available on the dashboard for coordinators, along with periodic reports.
An employee takes a mobile device from a docking station, where the device charges and synchronizes data and chooses an inspection round. The application automatically displays all tasks to fulfill. The system also works in areas without connection to IT networks, so the employee is able to do all the work without waiting for the internet connection, which is not always available in the plant. Since each device has its own 2D/RFID barcode, the employee does not have to search for it on the checklist. After scanning, the app displays what should be done in this certain place, and removes the task from the checklist.
Moreover, after an employee records the measured value, the app will inform them if it is acceptable in the measuring range (everything is defined flexibly by the inspection round's template - it can even be subject to the following conditions by the results of a certain device). That allows the discovery of an anomaly, even if the employee does not know the devices' characteristics. In case any disturbance occurs, they can create a service request, add a picture, a note, or record a voice message/sound- all from one place.
If further action is necessary, the device has synchronized contextual documentation associated with the barcodes. After scanning, e.g. cassette in switchgear, the employee receives access to the documentation of the particular cassette, with the division for the element list, single-line diagrams, etc.
After the inspection round, the only thing left is putting the device back on the docking station. At this moment, all the data (if work was carried out without a network connection) will be synchronized with the central server. And it is all done. The work is finished.


What is advantageous about this approach? Firstly, liquidation of paper documentation. Data is delivered to the central server. Measurements of particular points, even if they are carried out manually, create a historical database, which can be visualized and analyzed. It allows detection of disturbance or degradation of devices, which was impossible before.
The employees do not have to report the data manually- everything is registered in the system. The devices also possess tools that support the employee's work- the list of service requests and associated documentation. That makes the inspection round more effective, and the employees can immediately react, even if they cannot detect the problem themselves.
Inspection rounds' coordinators and the maintenance management receive detailed information about the plant's operation. The information that is usually not provided or gets lost. Integration of inspection rounds with the service requests guarantees that all the previously postponed requests do not get lost, and the repair work can be carried out faster.
All data related to other areas (inspections, DCS systems, and production data) is another advantage over the paper approach. The system informs about any measurement excess or errors (invalid states) and watches over doing inspection rounds according to the schedule. That results in a significant decrease in potential malfunctions and, at the same time, facilitates the work for all employees by saving hundreds of hours necessary while analyzing paper data.
Advantages of This Solution
- Getting rid of paper reports from inspection rounds.
- Inspection rounds schedules and their verification.
- Comparison of inspection rounds data and measurements history.
- Watching over the proper implementation of the inspection rounds- detecting disturbances and measurement inconsistency.
- Control points of inspection rounds- the necessity of scanning RFID barcodes.
- supporting the employees with the measurements list, signalizing deviations.
- Photographic documentation, audio during the inspection rounds.
- Integrated malfunctions reports and transmission to service requests module.
- Offline mode - tasks realization without access to a network, automatic synchronization,
- Possibility of linking the documentation and support during repair work.
Benefits
- Control over the schedule and realization of the inspection rounds.
- Digitalization of measurements and utilization of data for preventive actions.
- Supporting employees in work and sharing additional information.
- Certainty of carrying out the inspection rounds through control points.
- Integration with the service request module.
Solution Demonstration, Implementation, and Purchase
Contact Us
If inspection rounds functions seem interesting to you, feel free to contact us. AMAGE solutions are available in a number of implementation models, and importantly, you can start working with the system in a simple and attractively priced way with the LITE version.
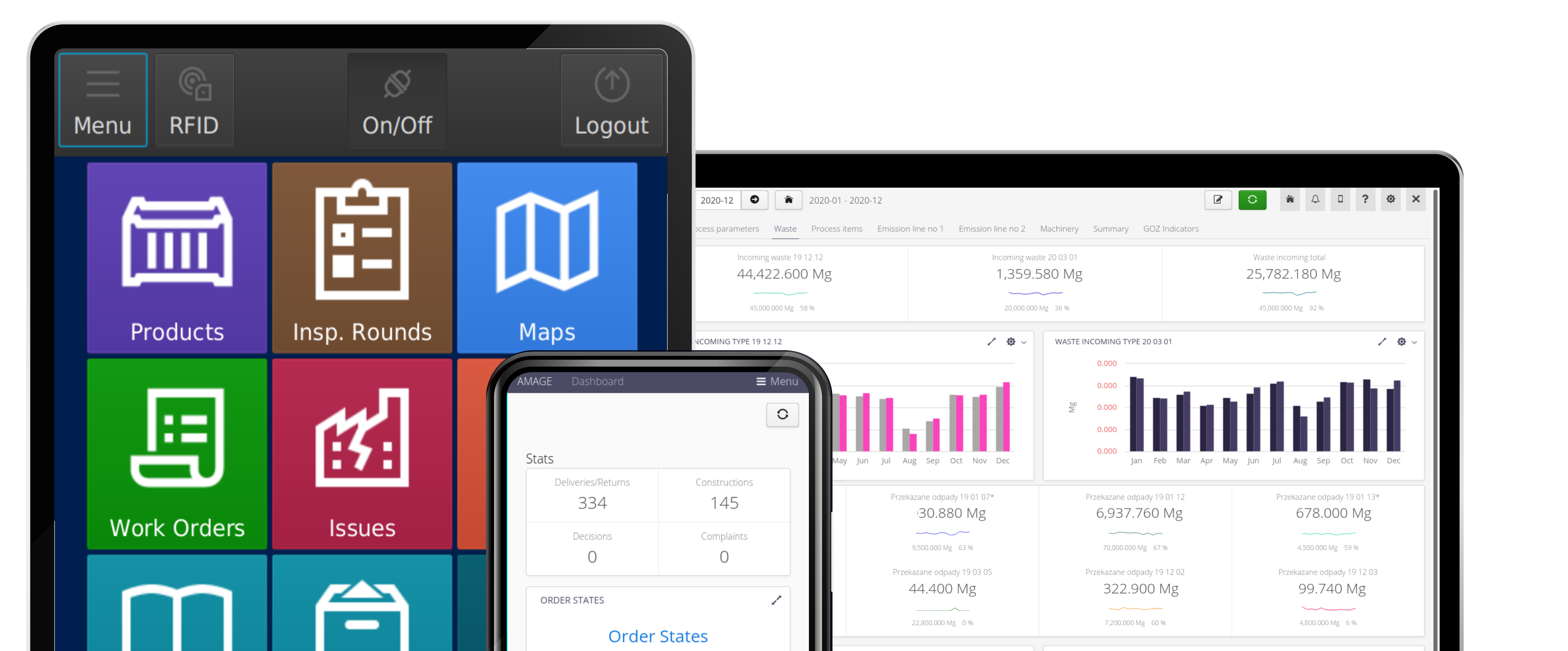