Meet the System – Inspections and Implementation of Inspection Works
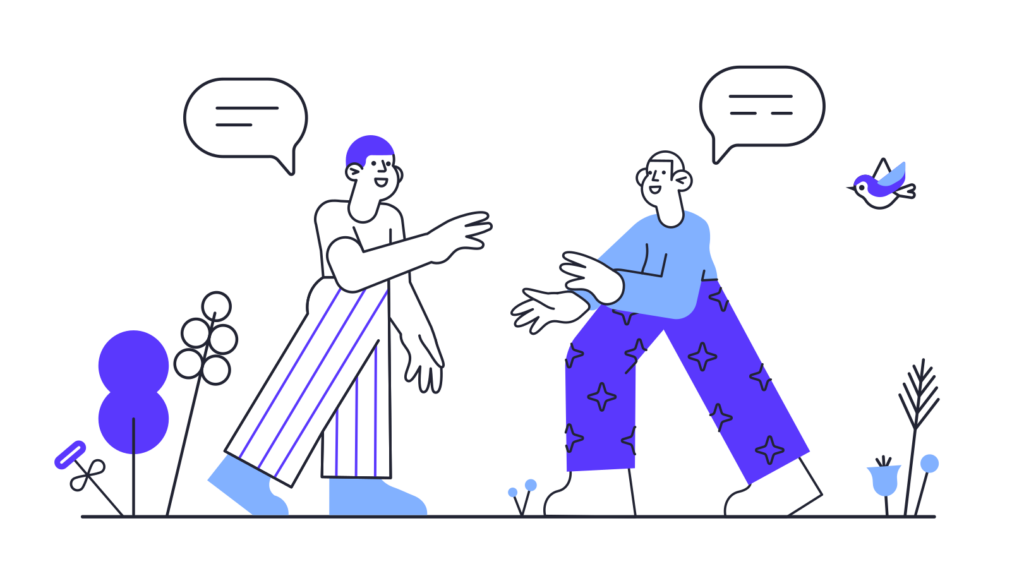
Industrial Plants Area
Inspections and Implementation of Inspection Works
Description
The solution allows for the management of inspection works concerning equipment located on-site with a fully electronic workflow of information during planning, execution, and generating final reports. The system consists of a management application and another dedicated to mobile devices, which supports the execution of inspection works at the equipment’s location.
The area coordinator can define templates for inspection works according to standards, guidelines, or DTR instructions. The template consists of configuration data, a set of questions and measurements to be taken, and tasks (scanning the badge, taking a picture, downloading the device configuration). With the help of such tasks, defined are the activities required to perform.
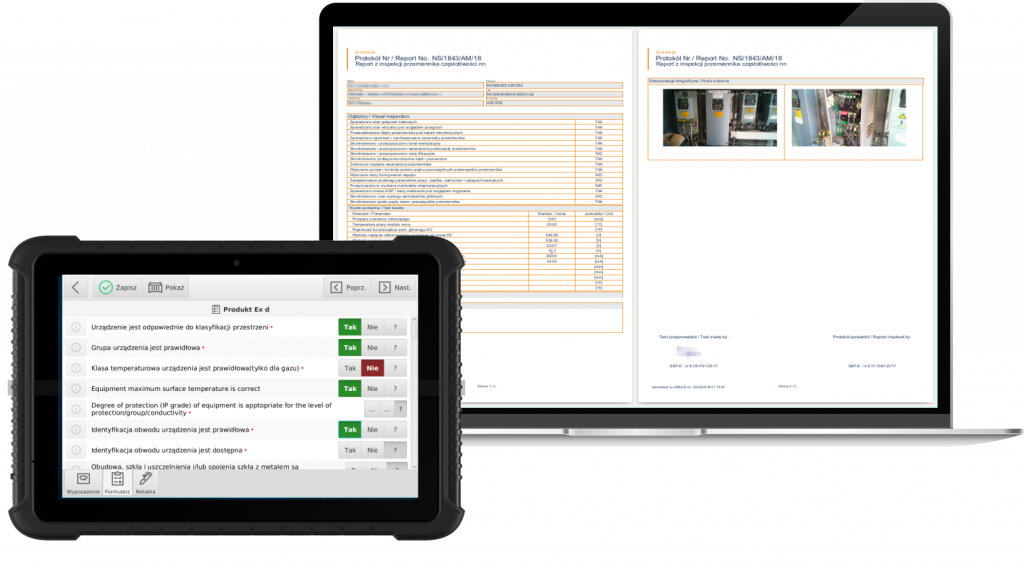
An additional element is the ability to specify the required stock materials for a given activity. That allows you to plan the necessary materials stock when performing these activities. The system also supports the definition of the required authorizations/admittances for employees crucial to allowing a given inspection to be performed.
The next step is to plan or create rules for establishing control works. That allows you to manually control the process and define the rules that will automate the control work, e.g., periodically every six months or based on parameters’ data, e.g., every 200 hours of operation (data entered manually or downloaded from devices). The execution of control work is carried out with mobile devices. The devices work online or offline (without network access synchronizing work at synchronization points). The user using 2D codes/RFID tags can quickly identify the device/inspection to perform.
The application guides the user through the activities. Measurements are supported by additional information suggesting the correctness of the results. RFID scan tasks allow you to further secure the implementation of works, for example, by mounting a badge inside the device. That will force the lids to open and execute the works. The system supports electronic signatures upon completion of execution and the process of acceptance of the implementation of control work. A flexible reporting mechanism for the current progress of work orders, grouping the control works, and reporting allows the generation of print-ready reports.
Advantages for the Coordinator
- Control and verification over planned and executed works for the coordinator.
- Full electronic circulation of information and activities for the coordinator.
- The unification of the methodology for conducting control work.
- Certainty of correct execution of works (before/after photos, read configuration, and ID).
- History of performed works linked to contracts/orders and individual devices.
- Automation of work scheduling (time-based, parametric).
- Automation of report generation with electronic signatures for the contractor. Consistent checklist for equipment, support in performing inspections, and prompting/verifying measurements as they are reported.
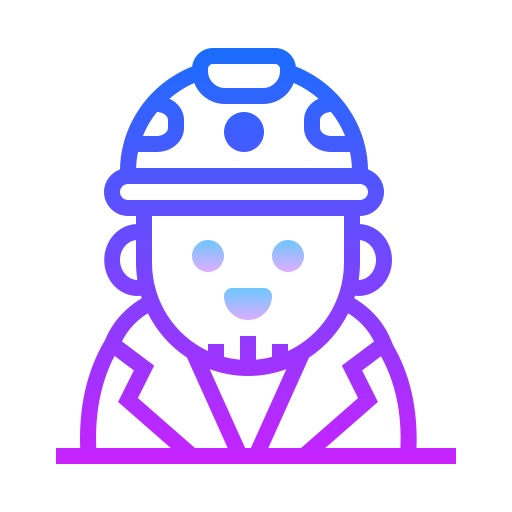
Advantages for the Contractor
- Full electronic flow of information and activities for the coordinator – the unification of the methodology for conducting inspection work.
- Linking to equipment (serial numbers, calibration dates) by scanning the equipment code (meters, measuring devices).
- Full electronic circulation of information, working in places without access to the network.
- No need to transcribe results in the office/after returning from tests
- Small and handy devices with a readable and user-friendly interface.
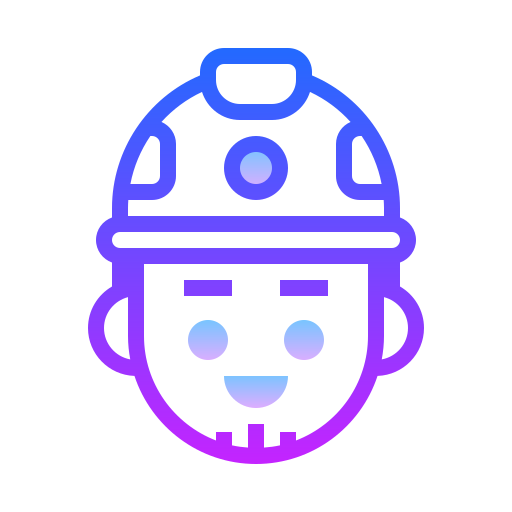
Value of Investment and Savings
- The costs of managing the performance of inspection work and control of schedules. Costs of damage to equipment/warranties for equipment without adherence to the inspection work schedule.
- The costs of equipment repair due to a lack of periodic inspection and based on inspection activities.
- Reduction of the costs of inspection/inspection works through intelligent scheduling, based on schedules, dates of work performed, and equipment operating data (e.g., hours of operations).
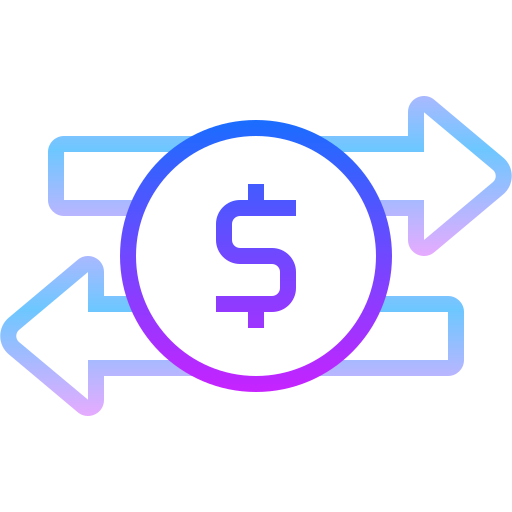
Users
- Inspection work contractor – performs inspection work using mobile devices, reviews the list of work to be done, and creates feedback (photos, configuration data).
- Maintenance Coordinator/Manager – defines inspection work templates, sets inspection schedules/parameters to automate work, analyzes and approves completed inspection work, and generates reports and statements.
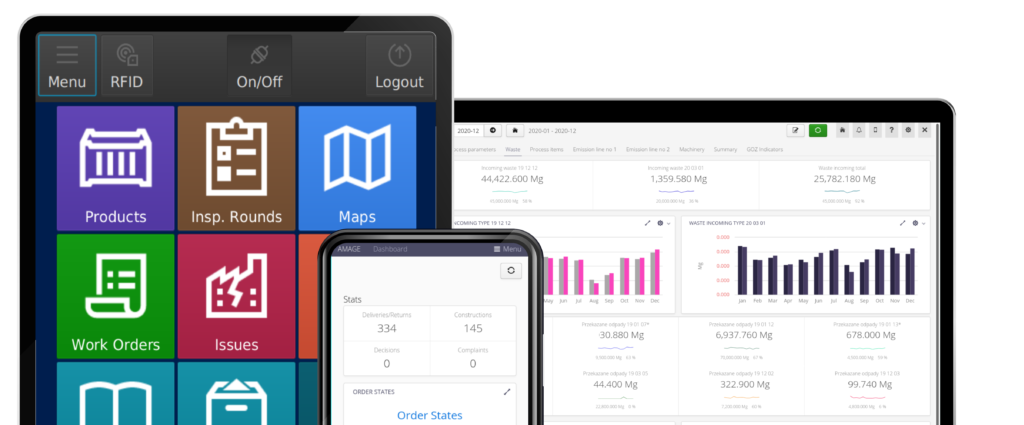
Components
- AMAGE Web Application
- AMAGE Shell – mobil execution
- AMAGE Fx – mobile execution
- Terminal/rugged tablet + docking station – offline access
- RFID identifiers – for checkpoints/device identification