Meet the System – Issues Handling Services
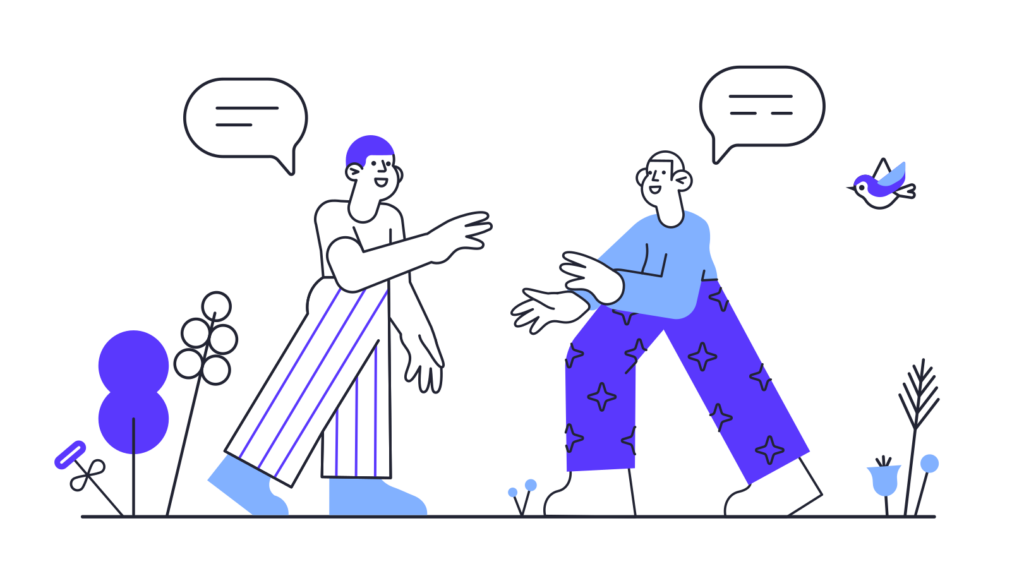
Industrial Plants Area
Internal and Event Handling Services
Description
The solution allows you to record all maintenance work, supervise its performance and control the cost of ongoing maintenance work. The system is designed with a simple and easy user interface. The coordinator is provided with a tool for a full analysis of the maintenance work carried out, including analysis of response times and parameters such as MTBF and MTTR.
The service work coordinator defines templates for service event states describing the process of requests from creation through handling to final billing. The coordinator has full control over the definition and additional parameters. The definition of service event type templates allows categorization of events (e.g., failure, error, defect, necessary inspection). After creating the basic data and importing the initial list of devices from Excel sheets, the system is ready to work.
Users via a browser interface, mobile application for phones, or dedicated ripstop mobile devices (rugged) can analyze reported service events. The system allows items retrieved from the warehouse or data from F- K systems such as invoices or accounting journals to be linked to a service event.
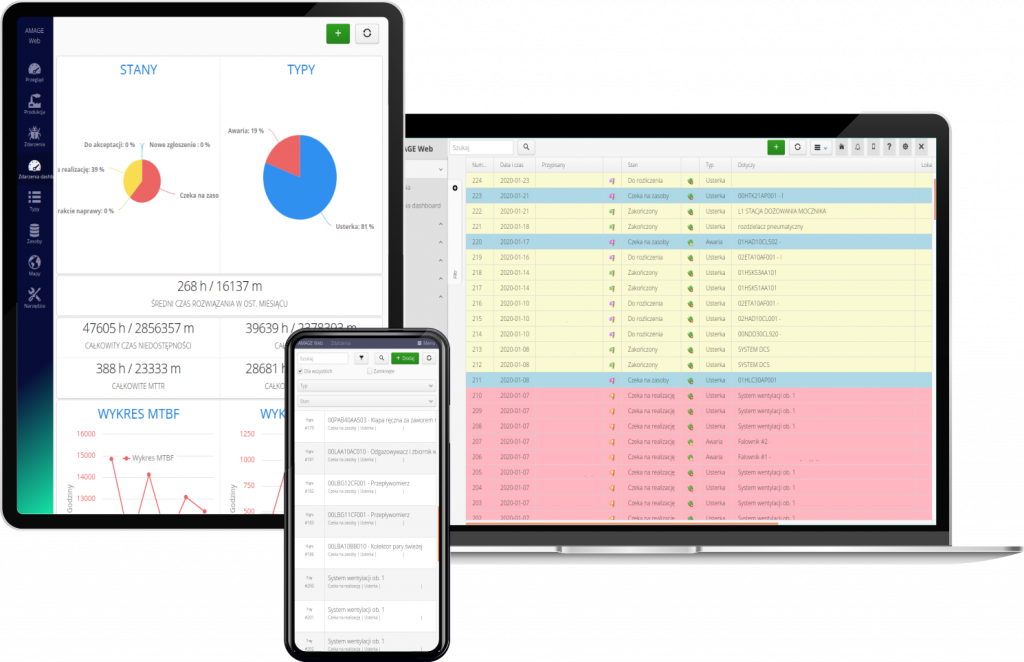
In addition, employees can log additional elements such as working hours to events, which allows full control of the finances associated with a given service event. Based on the events, the system can generate automatic notifications to users via email or internal user notification in the application (assignment to an event, leaving the event in a certain state for too long). Additional reports and visualizations allow for controlling other factors related to service events.
Advantages
- For everyone – simple and friendly user interface, only basic information and actions, interface adapted to the device on which it is run.
- For the coordinator – full control over the process of handling requests, definitions of the flow of events, and access to the system.
- For the coordinator – a set of analytical tools to control the implementation of control work and coordination of costs.
- For the notifier – a simple interface for reporting service events, multiple devices from which a service event can be created.
- For the contractor – simple interface and easy access to information, clear signaling of own work.
- For the contractor – the ability to group all additional factors in a service event – warehouse costs, taken materials, external invoices, and own labor hours.
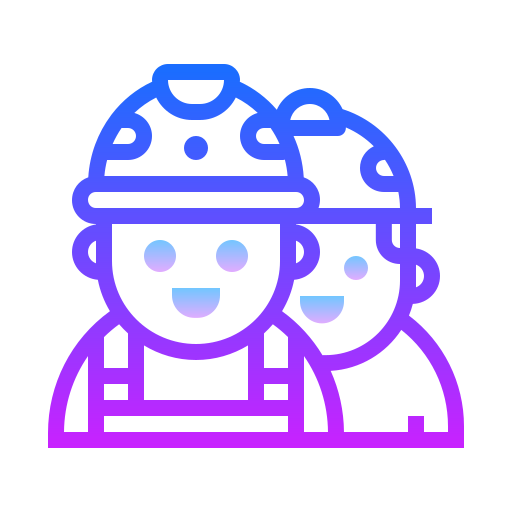
Value of Investment and Savings
- The Costs of plant downtime due to improper handling of service events (omission, lack of response, too late response).
- The Costs of maintenance work beyond the defined budget due to a lack of cost control from various sources.
- Protracted service work or downtime costs due to neglected response to all reported service events.
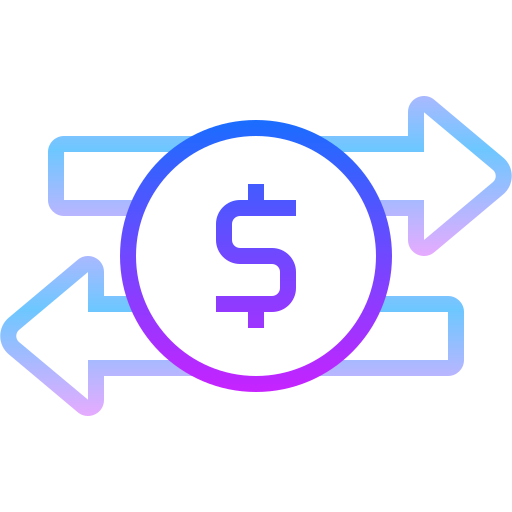
Users
- Notifier – reports a service event, describes the type, category and provides additional identification data
- Maintenance contractor – updates service events using mobile devices, reviews the list of events to be performed, creates feedback (photos, descriptions)
- Maintenance Coordinator/manager – defines templates for the flow of service events, the execution of work, and the cost of service work controls, and analyzes the performance and achievement of equipment reliability targets.
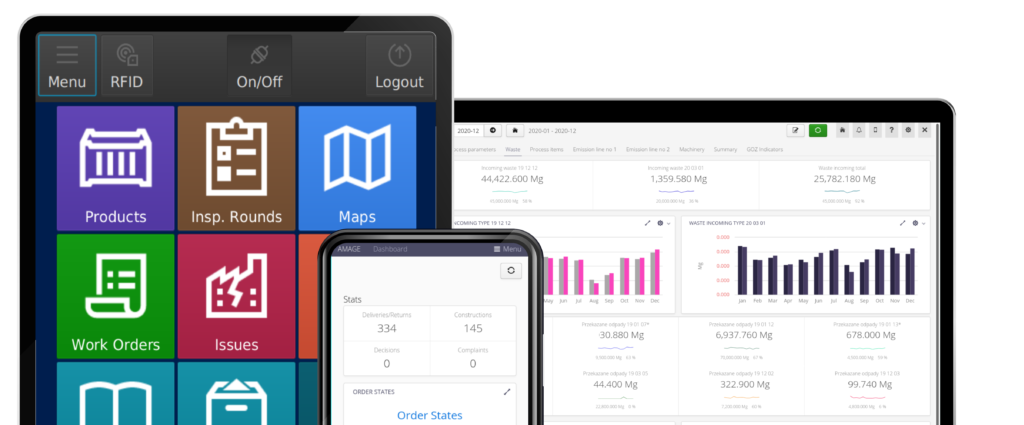
Components
- AMAGE Web Application
- AMAGE Shell App (Android) – mobile execution
- AMAGE Fx application – dedicated devices/offline use – mobile execution
- Terminal / tablet rugged + docking station – Fx Application Device
- RFID identifiers / 2D codes – for device identification and quick search for the device for which the service event is created