Meet the System – Monitoring and Data Acquisition
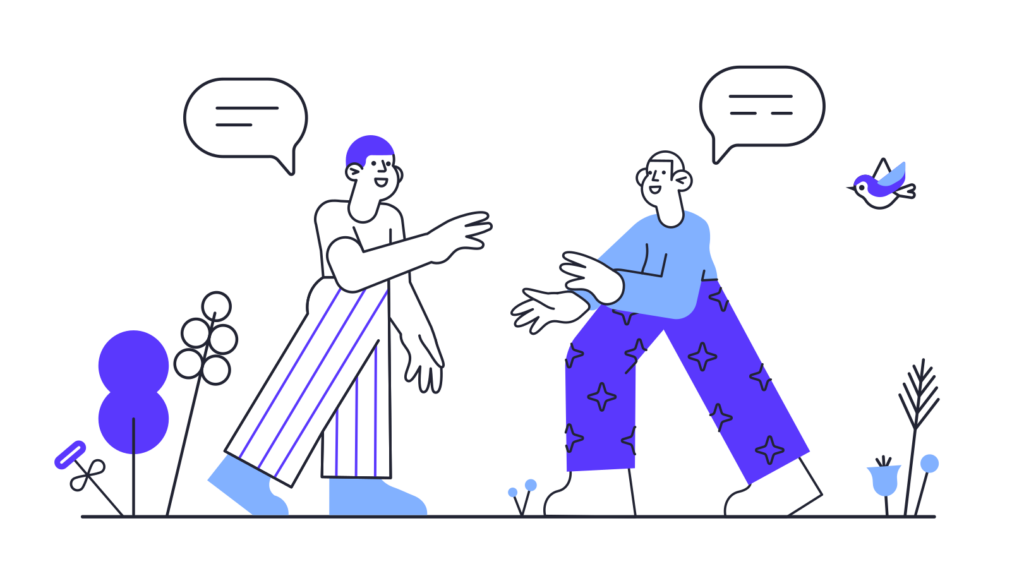
Industrial Plants Area
Monitoring of Equipment Performance and Data Acquisition
Description
The solution enables ongoing supervision of monitored devices through continuous communication and download of diagnostic data. Visualization mechanisms allow presenting the status of the devices, their internal state, and access to historical data through a web browser and mobile devices.
Alerting mechanisms allow users to be notified of undesirable events – exceedances of warning and alarm states, the occurrence of error codes, and the detection of excessive trends in the analyzed data.
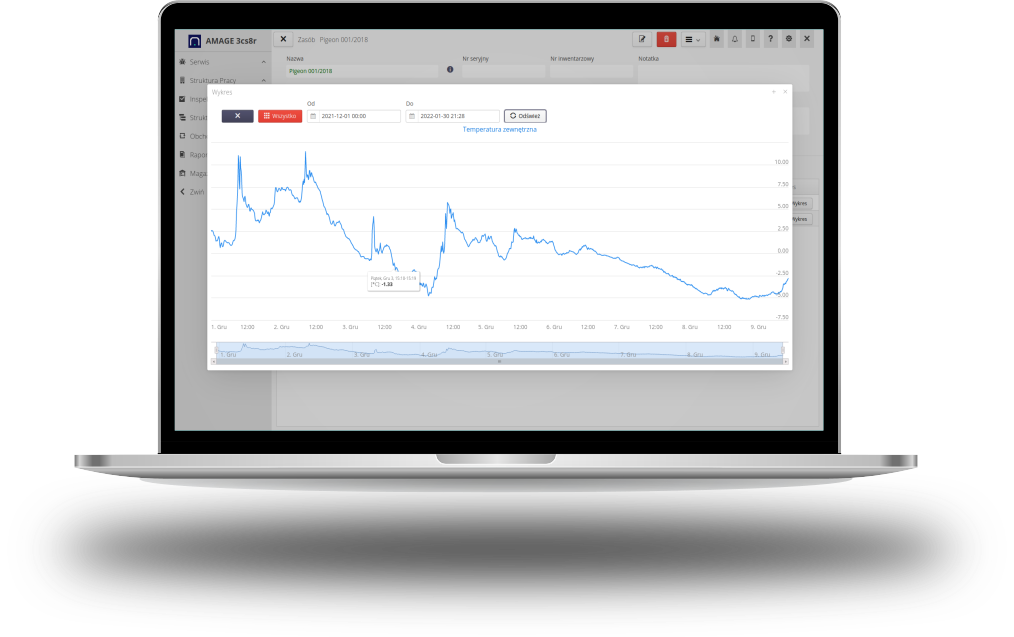
With the help of predefined controls, it is possible to control the operation of systems remotely by service teams until full diagnostics via dedicated solutions. Through data aggregation devices, it is possible to communicate with devices using communication protocols based on packet network (TCP/IP) and direct connections via RS-232/485 buses.
Data aggregation devices work as communication buffers and can act (for a limited time) as local data stores in case of communication loss with main servers. Aggregators can also work as edge-computing solutions dealing with preprocessing and transmission of filtered/aggregated data, e.g., low-bandwidth communication (cellular data communication networks – GSM/LTE-M). The system can be (and is recommended that it be) integrated with modules for service events, inspections, and rounds to fully collect data not only through automatic mechanisms of communication with devices but also through manual reporting of other noted deviations from proper operation. The system can be configured in such a way that external service teams (subcontractors) take care of supervision and maintenance work. The information available to those teams applies only to the equipment they supervise. All repair records are entered directly into the system.
Advantages for the Area Coordinator
- Visualization of equipment operation using systems accessible via web browsers and mobile devices. Access to current device data as well as historical data.
- Alerts for undesirable events during the operation of devices and the method of notification (notification inside the program, email, SMS).
- Defining external service teams responsible for the supervision of devices and providing them with a separate part of the system for supervision/monitoring and initial diagnostics of device operation. Directing alerts to external companies for more efficient maintenance.
- The ability to link the monitoring work with the modules of service events and inspections/inspection work, speeding up the realization of equipment supervision and implementing a fully electronic information flow on the operation of equipment/machinery.
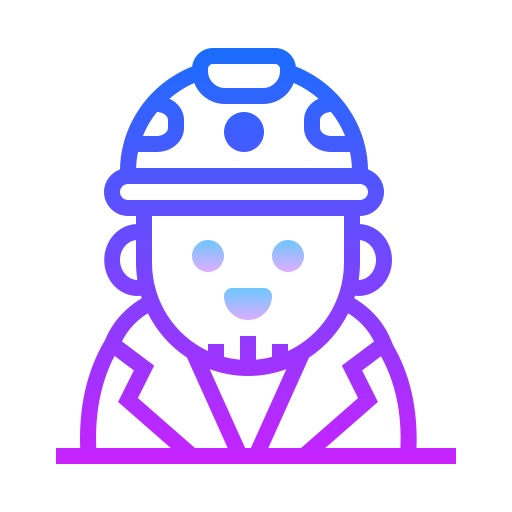
Advantages for an External Service Company
- Ability to remotely monitor equipment assigned to service, viewing current and historical data. Predefined control of equipment operation to minimize the effects of adverse events.
- Alerts and notifications of potential events on monitored equipment.
- Circulation of service and diagnostic information in the system – digitalized service events reports, inspection work, and annual reviews.
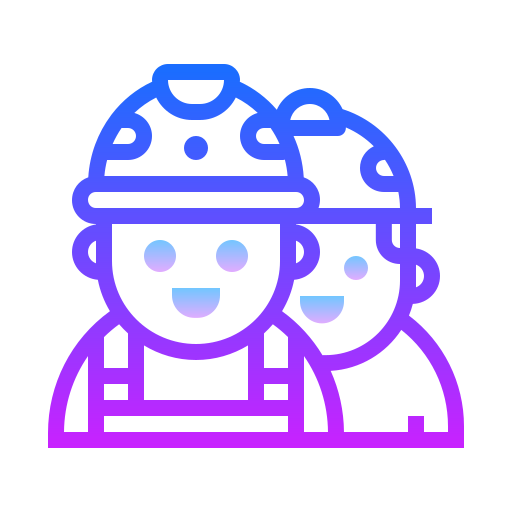
Investment Value and Savings
- Reduction of costs of repairing equipment previously undiagnosed – by analyzing trends, measurements, or error codes and not transferred to maintenance service.
- Reduction of in-house maintenance team costs by transferring supervision and service repairs of equipment to external companies supporting plant operations.
- Reduction of the costs of inspection and maintenance of equipment by integrating with the inspection work module, which will maintain an inspection and inspection work schedule according to the current operating parameters of the equipment (operating time, motoring hours, recent inspections, component failure rate) reducing the necessary work and activities.
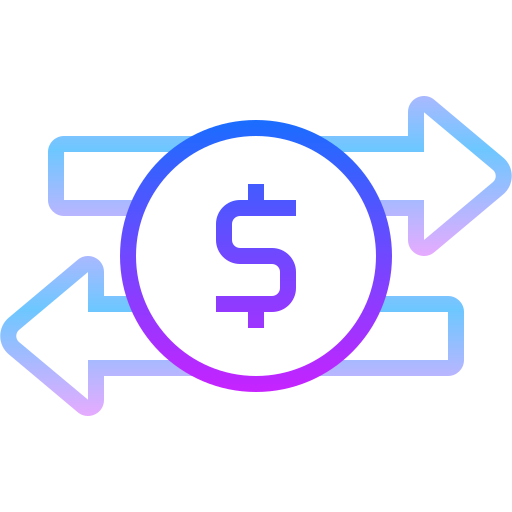
Users
- The maintenance coordinator – defines devices, measurements, visualizations, alerts, and notification methods. Reviews current and historical measurements. Monitors the work of the internal team and external service companies.
- Senior management – receives insight into device performance and historical data. Accesses visualization of equipment data from anywhere via web browsers/mobile devices.
- External service companies – monitor assigned equipment, respond to alerts and actions necessary for maintenance, report events, and control work directly in the system.
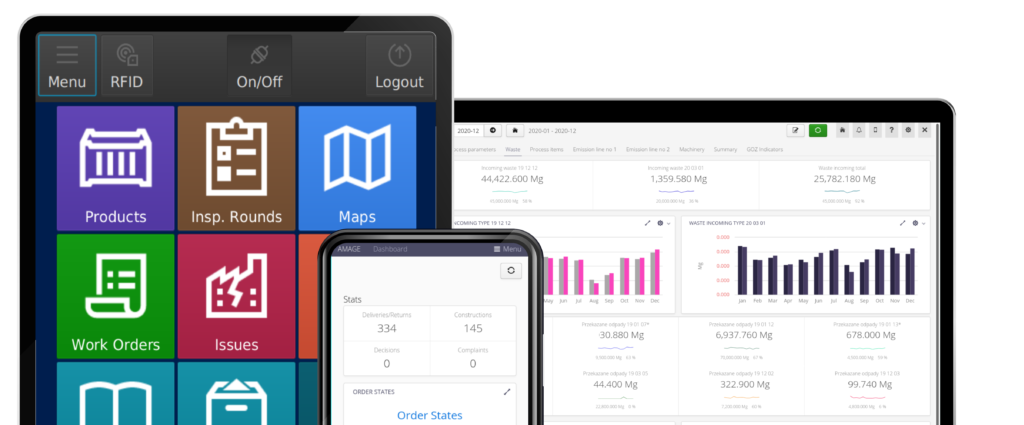
Components
- AMAGE Web Desktop Application
- AMAGE Shell Application
- Measurement data aggregators
- Measurement data synchronization server