Meet the System – Technical and Functional Rounds
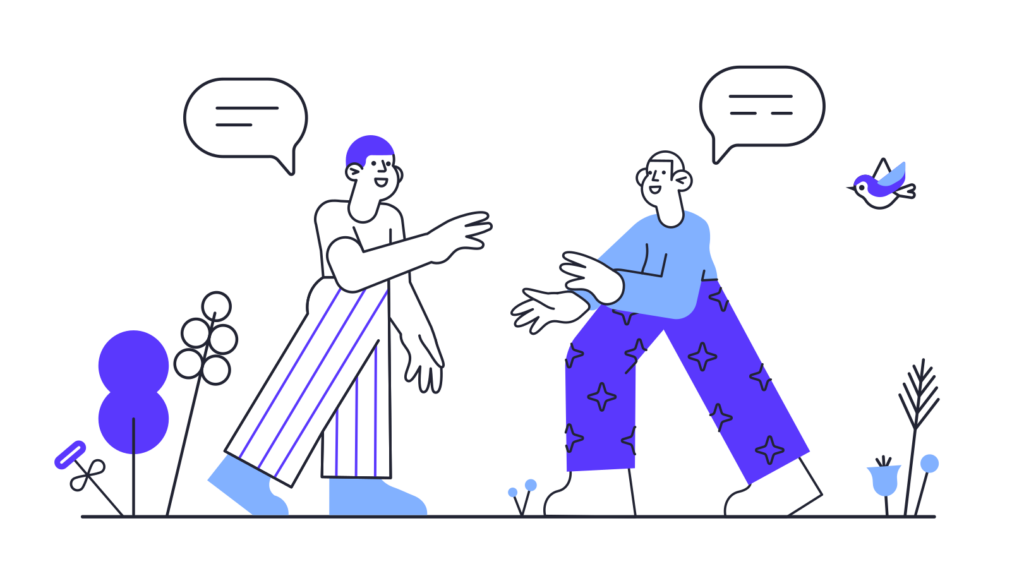
Industrial Plants Area
Technical and Functional Rounds – Registration of Periodic Activities
Description:
The solution allows scheduling and supervising the performance of technical rounds within the operation of an industrial plant. Coordinators define a list of equipment and points (locations) on the rounds routes. They create a walk-around checklist, which consists of: questions (“Is the device working correctly ? Boiler status ?”), measurements (“Read the temperature in line X”), and tasks (“Scan the RFID code at checkpoint A”). Each of these elements has additional features and functions.
The scanning uses placards mounted on the routes equipped with 2D codes or RFID tags. Once the checklist is built and a schedule for making rounds (e.g., every 6 hours) is defined, along with acceptance parameters (+/- how many hours we give the margin for execution). After launching such a template, users by mobile devices can perform a given workaround. The mobile app helps in the execution by marking points already visited and pointing out potential measurement errors.
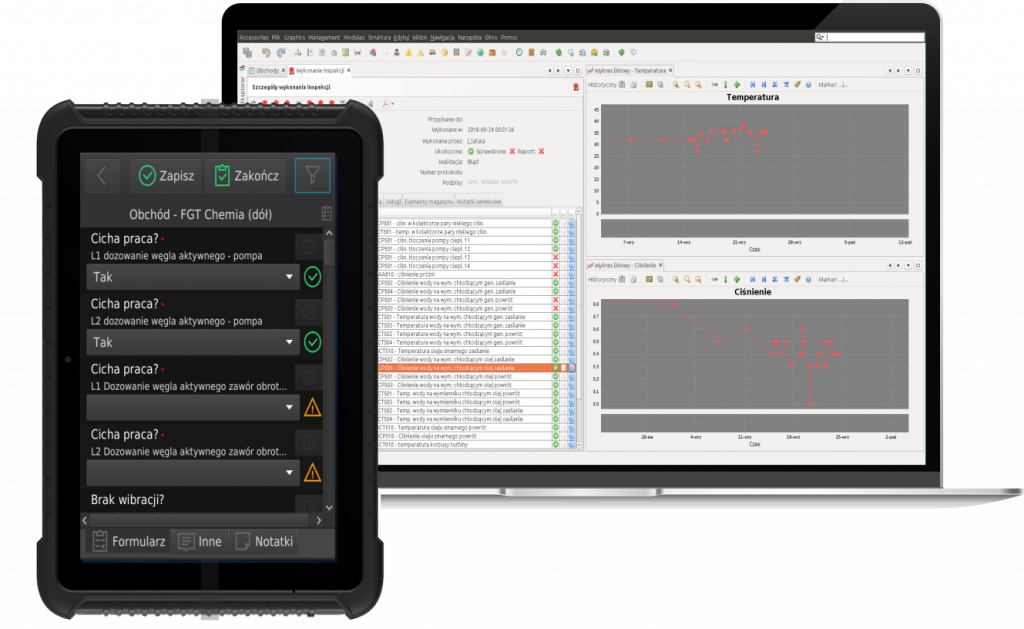
After making the rounds, all the data returns to the central system. Mobile applications work online (we send data to the server all the time) as well as offline (we send it after the work is completed after putting it on the docking station). Coordinators receive information after the rounds are made. It is possible to aggregate data from successive rounds (charts, reports), detect performance errors (wrong answers, exceeded measurements), and generate reports on the implementation of rounds by employees (timeliness of completion, attendance at checkpoints). The system generates information in the form of emails and notifications in the application on key parameters (reports, exceedance alerts).
Advantages for the Coordinator
- Certainty of making rounds through RFID checkpoints.
- Control over the timeliness of rounds for the coordinator – access to historical data and its analysis.
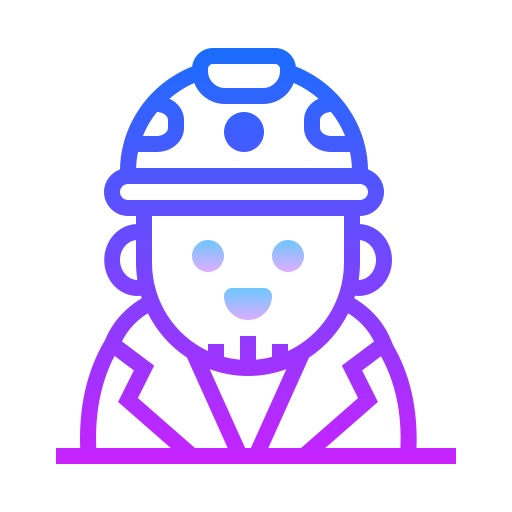
Advantages for the Contractor
- Getting rid of filling out paper cards.
- Contextual information about devices (attached documentation, maps).
- Information about potential erroneous measurements and damage to equipment.
- Reminder to perform rounds.
- Small and handy devices with a clear and simple interface.
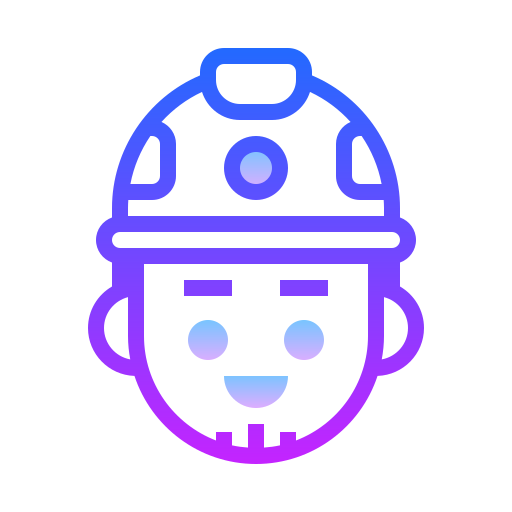
Value of Investment and Savings
- The costs of not supervising the rounds and damage to equipment during this time – rounds not made, falsified reports, making rounds “on the desk”.
- The costs of not having access to historical information and detecting potential changes in measurement data not detected by a single measurement.
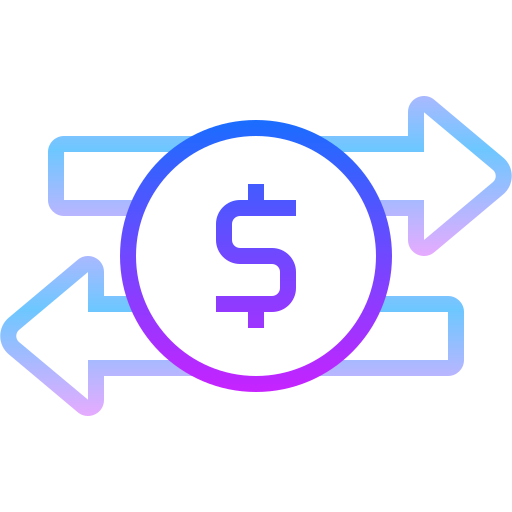
Users
- Workaround contractor (workaround) – performs workarounds and records history using mobile devices.
- Maintenance Coordinator/manager – creates/modifies rounds paths, defines rounds work schedules, verifies work execution, analyzes activities and measurement results.
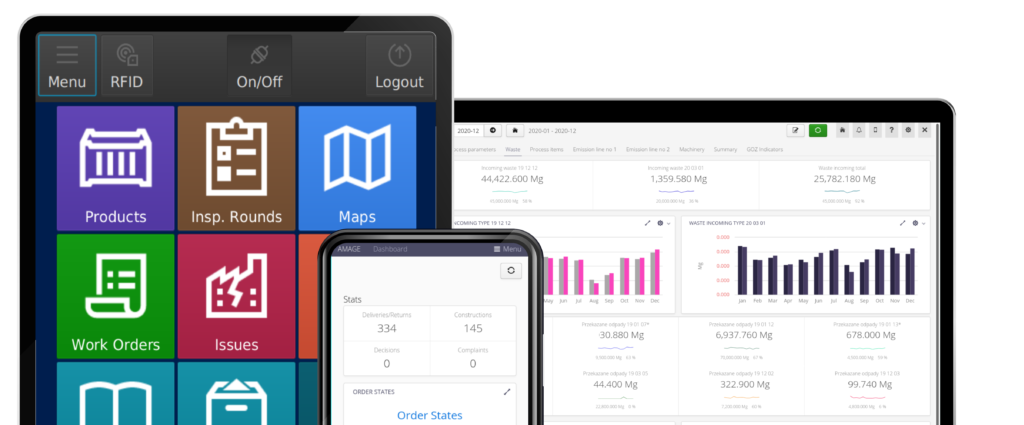
Components
- AMAGE Web Desktop Application – for the coordinator – data management and viewing
- AMAGE Fx application – for the artist (dedicated devices) – performing the main activity via mobile interface
- Terminal / tablet rugged + docking station – a device with the Fx application
- Control labels / plates – RFID technology, 2D codes for identification of control points